Le auto del futuro saranno fatte con gli scarti del petrolio?
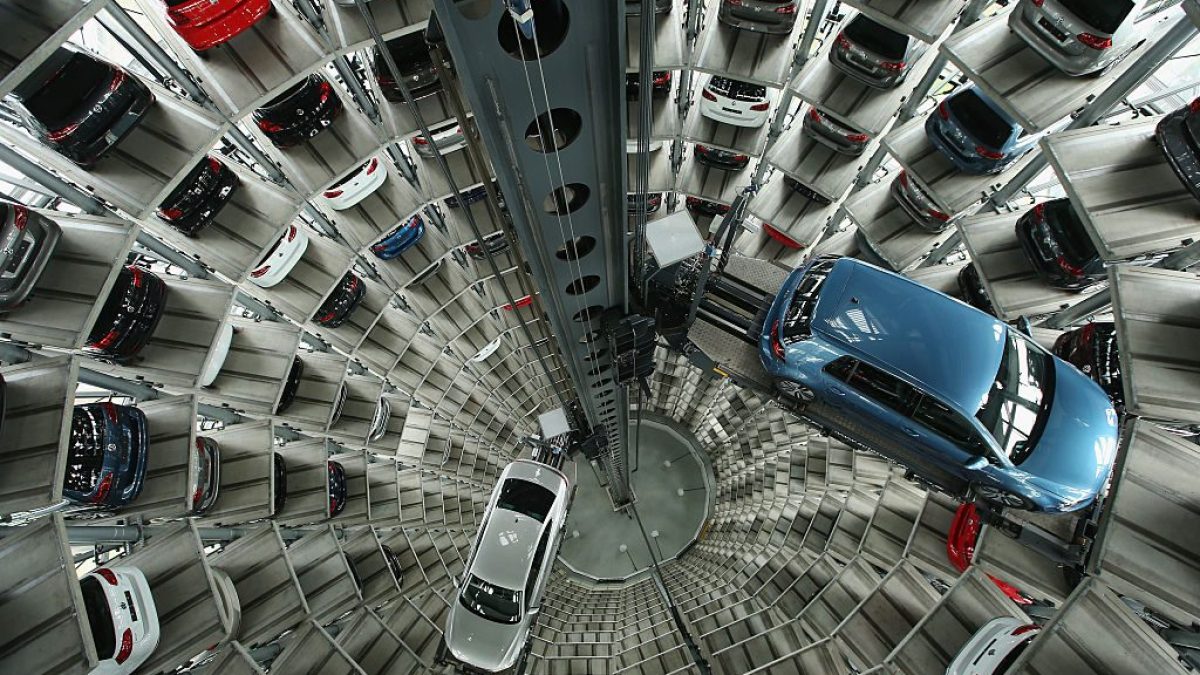
Ridurre le emissioni di gas serra e migliorare l’autonomia dei veicoli elettrici, ma anche utilizzare materiali sempre più leggeri, che siano abbastanza resistenti da poter essere impiegati al posto di quelli tradizionali: è questa la direzione verso cui si sta muovendo l’industria dell’auto che negli ultimi anni ha ampliato l’uso della fibra di carbonio, un materiale che combina un’eccezionale resistenza con un peso ridotto, pur dovendo limitarne l’utilizzo ad elementi strutturali di vetture di lusso perché significativamente più costoso di acciaio e alluminio. I ricercatori del Massachusetts Institute of Technology (MIT) hanno però sviluppato un modo per ricavare questa fibra da una materia prima particolarmente economica, ottenuta dagli scarti del processo di raffinazione del petrolio, un residuo che attualmente è impiegato in applicazioni di basso valore, come la fabbricazione di asfalto e bitume.
Oltre ad essere più economica da produrre, la nuova fibra di carbonio offre un vantaggio aggiuntivo rispetto a quella convenzionale a base di poliacrilonitrile, in quanto per sua natura è resistente alla compressione, il che supporta un utilizzo più esteso. Il processo di sintesi di questa nuova fibra è stato descritto sulla rivista Science Advance dal team di ricerca del MIT che, dopo circa quattro anni di lavoro, in risposta a una richiesta del Dipartimento dell’Energia degli Stati Uniti volta a individuare un modo per rendere le auto più efficienti e ridurne il peso complessivo, ha proposto un percorso di fabbricazione di una nuova fibra. L’ente federale sta spingendo per lo sviluppo di materiali strutturali leggeri, che corrispondano agli standard di sicurezza degli odierni panelli in acciaio, ma che possano essere realizzati a un prezzo sufficientemente basso da poter potenzialmente sostituire del tutto l’acciaio dei veicoli.
“Se guardiamo le auto di oggi rispetto a quelle di 30 anni fa, il loro peso è aumentato di oltre il 15 percento all’interno di uno stesso segmento – ha affermato Nicola Ferralis, ricercatore del MIT e autore corrispondente dello studio – . Un’auto più pesante richiede un motore più grande, freni più potenti e così via, quindi la riduzione del peso della carrozzeria o di altri componenti ha un effetto a catena che determina un ulteriore risparmio di peso”.
Come premesso, uno dei principali motivi per cui l’uso della fibra di carbonio nelle vetture è limito a pochi modelli molto costosi è che, per raggiungere la qualità necessaria per l’impiego in questo settore, sono necessari materiali e processi particolarmente onerosi. La fibra di carbonio attualmente utilizzata costa dai 20 ai 25 dollari al chilo, spiega Ferralis, e “può esserlo molto di più”, fino a centinaia di dollari al chilo per applicazioni specifiche, come per la produzione di componenti per i veicoli spaziali. A incidere sul prezzo, oltre al processo produttivo in sé, è la poliacrilonitrile, che si ottiene da un prodotto petrolifero raffinato e trasformato, e può rappresentare oltre il 60% del costo finale della fibra. Utilizzando invece gli scarti della raffinazione, un materiale chiamato pece del petrolio, è chiaramente possibile abbattere il costo del polimero.
Il processo produttivo per realizzare la fibra di carbonio dalla pece è “estremamente minimo, sia in termini di fabbisogno energetico sia in termini di elaborazione effettiva da eseguire” ha aggiunto Ferralis che, insieme ai colleghi, si è avvalso di simulazioni di dinamica molecolare per esplorare l’elaborazione e lo spazio delle fasi chimiche necessarie, attraverso una struttura di modelli di fibra di carbonio per identificare gli effetti sulle prestazioni.
“ll nuovo processo che stiamo sviluppando non ha solo un effetto sui costi di produzione ma potrebbe aprire la strada a nuove applicazioni” precisa Ferralis che ha sottolineato come il nuovo percorso possa anche ovviare a parte delle complicazioni di fabbricazione dei compositi di fibre convenzionali, inclusa la trasformazione in un tessuto e la disposizione secondo schemi precisi, necessari “per compensare la mancanza di resistenza alla compressione”. Si tratta dunque di una soluzione ingegneristica che permette di superare le carenze del materiale mediante un nuovo processo, grazie al quale, ha concluso Ferralis, tutta quella complessità extra non sarebbe più necessaria.